O processo construtivo no Brasil, após longo período de lento desenvolvimento, tem evoluído significativamente.
O contínuo crescimento do mercado da construção metálica foi incrementado pela expansão e modernização dos fabricantes de estruturas metálicas. Tal cenário tende a uma evolução ainda maior devido à efetivação de novas plantas, dotadas de equipamentos modernos e de alta eficiência.
A automatização e modernização do parque fabril têm melhorado significativamente a produtividade das fábricas e propiciado maior qualidade aos produtos, que atinge atualmente os mesmos padrões da indústria Européia.
Equipamentos robotizados de corte de tubos de última geração, capazes de executar em uma só operação e com alta produtividade as “bocas de lobo” das peças de seção circular e os chanfros especificados no projeto, foram adquiridos por diversas empresas do setor e por empresas voltadas à prestação de serviços. Outros equipamentos para a produção de estruturas tubulares foram desenvolvidos com significativos resultados. Como exemplos, alguns equipamentos são mostrados nas figuras 1 e 2.
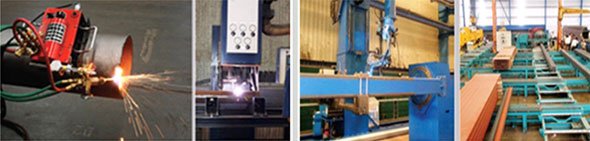
Fig. 1 e 2 – Equipamentos e automatização da fabricação de estruturas metálicas
No momento vislumbra-se a execução de muitas obras que serão necessárias em decorrência da Copa do Mundo de Futebol de 2014 e das Olimpíadas de 2016 que serão realizadas no Brasil. Espera-se que estas obras tragam consigo novos aprendizados e sejam elementos facilitadores para o desenvolvimento de nossa engenharia como um todo.
O desenvolvimento da construção civil levou o setor a buscar alternativas construtivas com mão de obra mais qualificada nos canteiros de obra. Desta forma, grande parte dos serviços artesanais até então executados são substituídos por processos industrializados, com ganhos na qualidade dos produtos finais e na produtividade final da edificação.
O processo de industrialização pode parecer introduzir maior custo, porém, como nos demais processos industriais, a produção em série melhora a cada dia sua performance, tornando seus custos mais atrativos.
Como em todos os processos industriais um bom planejamento inicia-se com a elaboração de todos os projetos e é nesta fase que as definições do empreendimento devem ser tomadas. Começa aí a maior valorização do projeto como um todo e como conseqüência dos profissionais da engenharia e a arquitetura nacional.
Esse prévio domínio da tecnologia de construção e o conhecimento antecipado de todos os detalhes, dificuldades, materiais recomendados, quantitativos, custos, etc., permitem soluções antecipadas e bem engenhadas. Imperfeições construtivas e definições de última hora ficam minimizadas e com isso os ganhos provenientes das reduções das perdas são muitos.
A definição dos materiais a serem empregados na estrutura, compostas por elementos preferivelmente pré-fabricados, leves, de fácil manuseio, sem risco de quebra e perdas, com formas harmônicas e simples são a melhor opção e, nesse caso, as estruturas metálicas levam larga vantagem.
Estruturas moldadas “in loco” com grandes consumos de mão de obra no campo, grandes desperdícios de materiais, inclusive de madeiras, geralmente pouco precisas e estruturas robustas, com ligações não bem definidas e de aspecto pesado, grosseiro, não se adéquam a obras onde se exige também um maior apelo estético. Essas estruturas tendem cada dia mais, a perder espaço no novo cenário da construção nacional.
Dentro desse contexto, a estrutura metálica tem muito a oferecer aos construtores e empreendedores, a exemplo do que acontece em países desenvolvidos, onde ela é responsável por cerca de 60% dos empreendimentos.
Uma adequada orientação de especialistas ajudará muito na boa avaliação do processo. Nessa avaliação o empreendimento deve ser visto como um todo, com custos apropriados desde os primeiros serviços nos canteiros de obras. Reduções no número de fundações devido aos maiores vãos, da carga total da edificação, do desperdício, dos prazos construtivos, de despesas na administração da obra, canteiros limpos e organizados além do retorno antecipado do capital, etc., devem ser valorizados.
Perfis tubulares

Fig. 3 e 4- Tubos sem costura e tubos com costura
É crescente nos países desenvolvidos e também aqui no Brasil a utilização das estruturas metálicas tubulares e para o entendimento desta opção é necessário conhecer mais de perto esses materiais.
Os tubos empregados nas estruturas metálicas podem, em geral, ser qualificados basicamente em dois grandes grupos que são:
- Tubos laminados a quente (figura 3), provenientes de um processo de perfuração a altas temperaturas de uma barra circular maciça de aço, gerando assim um produto sem emendas e uniforme em toda sua extensão e na seção transversal;
- Tubos com costura (figura 4) que são produzidos a partir de chapas planas conformadas a frio e soldados, com solda longitudinal ou helicoidal.
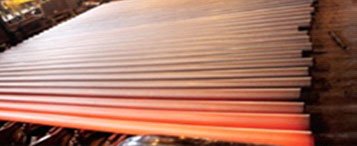
Fig. 5 – Leito de resfriamento
Após o processo de laminação, os tubos resfriam-se lentamente até a temperatura ambiente e por ter sua massa uniformemente distribuída em torno de seu eixo longitudinal, este resfriamento é homogêneo ao longo de toda seção transversal e de seu comprimento, não existindo assim valores significativos de tensões residuais, proveniente de gradientes de temperatura (figura 5).
Por este motivo, conceituadas normas internacionais consideram esta característica dos tubos laminados a quente de forma particular.
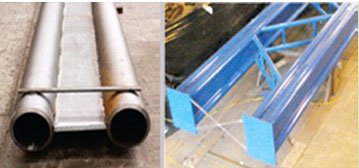
Fig. 6 – Composição de tubos
Comportamento dos tubos frente aos esforços solicitantes
Em função de sua geometria e dos baixos níveis de tensões residuais, os tubos laminados a quente ou tratados termicamente apresentam ótimo comportamento aos esforços de compressão axial. Conceituadas normas como a Européia e a Canadense tratam estes produtos de forma diferenciada.
Entretanto, para esforços de flexão, os tubos de seção transversal circular não apresentam a mesma performance que na compressão e, por esse motivo, como elementos isolados, não são a melhor opção. Para esse esforço, a forma ideal de aplicação do tubo é através da composição de dois ou mais tubos através de treliçamentos ou com o emprego de chapas, formando uma seção semelhante a de um perfil I ou outras seções fechadas, cujas mesas são constituídas por tubos (figura 6).
O emprego de treliças tubulares planas ou espaciais (figura 7), onde as barras que as constituem estão predominantemente solicitadas por forças axias de tração ou compressão é a opção mais tradicional. Essa solução é comumente empregada em estruturas de grandes vãos devido a seu baixo peso e bom desempenho.

Fig. 7 e 8- Treliças tubulares planas ou espaciais e treliças mistas
Também como barra fletida mista, onde o banzo superior trabalha solidariamente com a laje, ligado por conectores de cisalhamento (figura 8), obtêm-se resultados muito atrativos. Nesses casos as treliças podem ser dimensionadas de forma a resistirem todas as cargas que irão ocorrer na fase construtiva, o escoramento da estrutura e da própria laje. Esse modelo implicará em grande flexibilidade para a construção, mantendo as vantagens do sistema treliçado.
Nesse tipo de solução, as passagens de dutos de utilidades junto à laje ficam facilitadas, o que também simplifica sua execução.

Fig. 9 – Perfis retangulares
Os tubos com seções transversais retangulares (figura 9) são também uma boa opção como barras fletidas. São provenientes da conformação a frio das seções transversais circulares. Quando posteriormente tratados termicamente para redução das tensões residuais, introduzidas pelo processo de conformação a frio, apresentam comportamento muito similar aos tubos laminados a quente, o que os diferencia dos que não passaram por esse processo.
Na flexão as seções retangulares apresentam melhor desempenho que os tubos de seção circular. Apesar de não ser a melhor seção para este tipo de esforço, sua forma geométrica simplifica ligações. Seções retangulares são esteticamente mais agradáveis que outras seções abertas e propiciam ótimo acabamento às edificações, tornando-as assim uma boa solução, tanto quando empregadas como barras que compõe treliças como quando usadas como vigas. Podem também serem ligadas às lajes de concreto por intermédio de conectores de cisalhamento, melhorando consideravelmente sua performance à flexão. O dimensionamento dessas vigas mistas, com pequenas adaptações, é feito conforme prescrito na ABNT NBR 8800 para as seções abertas.
Outro fator que favorece a estrutura tubular é seu menor custo de pintura e/ou material de proteção contra incêndio. As menores áreas de pintura e/ou material de proteção contra incêndio das seções fechadas (cerca de 52% da área do perfil de seção aberta equivalente – Apint tubo ≈ 3,14D e Apint H ≈ 6D) é outro ponto que deve ser considerado na análise de custo do projeto.
Projeto de norma brasileira de estruturas de aço com perfis tubulares
Uma nova norma brasileira sobre estruturas de aço e mistas de aço e concreto com perfis tubulares está em desenvolvimento na ABNT e espera-se que no próximo ano já se tenhamos mais esta ferramenta fundamental para o crescimento tecnológico nacional. Essa norma, complementar à ABNT NBR 8800:2008, pretende cobrir as lacunas ainda existentes no projeto, fabricação e montagem de estruturas metálicas, abordando aspectos peculiares aos tubos, com grande foco nas ligações tubulares, estruturas mistas e soldas, dentre outros assuntos.
Ligações
As ligações das estruturas tubulares, anteriormente consideradas como principal gargalo a essa solução construtiva, estão se tornando mais corriqueiras para projetistas e fabricantes.
Sejam elas projetadas e executadas por intermédio de chapas de ligação; sejam em boca de lobo, as ligações deixam de ser um obstáculo e passam a integrar a uma rotina do ambiente estrutural.
Essa mudança cultural acompanhada pelo processo produtivo altera o conceito das estruturas tubulares, antigamente dominado pelas estruturas espaciais, muito densas e carregadas visualmente, com nós complexos e, em muitos casos, pesados, e que agora cedem espaço às estruturas tubulares planas e multiplanares, visualmente mais limpas e atrativas (figura 7).
Os projetistas exercem papel fundamental neste momento do desenvolvimento de nossa cultura tubular, pois são responsáveis pelas definições das formas e das ligações das estruturas. Sua capacidade de projetar de forma simples, aliada à experiência profissional pode simplificar significativamente os serviços de fabricação, gerando assim menores custos de produção. Soluções com menor número de operações de fabricação, mesmo que conduzam a um maior peso estrutural, podem ser mais econômicas. Nestes casos é sempre conveniente o contato com o fabricante da estrutura que certamente saberá avaliar melhor as alternativas apresentadas.

Fig. 10 – Ligação de tubo de seção transversal circular com chapa de extremidade
Nos exemplos da Figura 10 podemos comparar o número de operações realizadas na fabricação das duas ligações com chapa. No caso da Figura 10 (a) a primeira operação será rasgar o tubo longitudinalmente para que a chapa de ligação possa entrar na seção do tubo. A chapa de ligação é cortada e furada, sendo a seguir posicionada para soldagem. Apos a soldagem da chapa de ligação no tubo, os dois tampões em forma de semi-círculo são cortados e posteriormente soldados em torno do tubo vedando assim a abertura existente.
A solução adotada na Figura 10 (b), quando possível de ser empregada, é extremamente mais simples que a anterior, uma vez que requer apenas a fabricação da seção “T” que será o elemento de ligação (podendo esta seção “T” ser obtida pela composição de chapas ou pelo corte de um perfil “I” soldado ou laminado), a execução da furação e da soldagem dessa seção “T” no tubo.
Aços
Como em todos os sistemas construtivos, a especificação do aço estrutural é relevante e no caso das estruturas tubulares a correta especificação do aço estrutural é uma boa prática. Normalmente, para ambientes agressivos, quando especificamos os aços ASTM A 500 (Standard Specification for Cold-Formed Welded and Seamless Carbon Steel Structural Tubing in Rounds and Shapese) e ASTM A 501 (Standard Specification for Hot-Formed Welded and Seamless Carbon Steel Structural Tubing), é recomendável vedar as extremidades dos tubos, impedindo assim a entrada de ar, o que garantirá proteção contra corrosão interna no tubo, dispensando assim qualquer outro tipo de proteção. A adoção de aços patináveis, é outra possibilidade muito interessante e neste caso os aços ASTM A618 (Standard Specification for Hot-Formed Welded and Seamless High-Strength Low-Alloy Structural Tubing) e ASTM A847 (Standard Specification for Cold-Formed and Seamless High-Strength, Loe-Alloy Structural Tubing with Improved Atmospheric Corrosion Resistance) são os mais utilizados.
Neste momento de crescimento, quando começamos a trabalhar com estruturas tubulares, já mais tradicionais em países do primeiro mundo, é primordial que as experiências adquiridas sejam transmitidas aos novos usuários, que a cultura seja disseminada e que tenhamos sempre abertas nossas mentes para o aprendizado e a inovação. As universidades, a indústria e nós profissionais, somos os principais responsáveis por tal disseminação. Precisamos ser estimulados por novos desafios, mas temos o dever de levar aos principiantes os aprendizados até aqui adquiridos.