Apesar de ser utilizado para os mais diversos fins há mais de 100 anos na Europa e outros países mais industrializados, somente na década de 60, o alumínio teve seu início como elemento estrutural no Brasil. Trabalhos pioneiros do engenheiro austríaco Hans Egger e mais tarde do anglo-canadense Cedric Marsh abriram um grande mercado ora inexistente, da aplicação do alumínio em estruturas metálicas em nosso país, tornando-o o mais profícuo do mundo nessa área.
O alumínio tem a densidade de 1/3 da do aço.
Devido ao seu baixo peso próprio, ele se torna um excelente material para não só estruturas móveis como também estruturas estáticas, onde o peso próprio tem fundamental importância nas cargas totais do projeto. Assim também evidencia a vantagem sobre o aço na fabricação, transporte e montagem.
Devido a suas características próprias, o alumínio é dentre os materiais comercialmente encontrados o de maior taxa resistência/peso. Portanto, o uso do alumínio em perfis estruturais pode proporcionar uma estrutura metálica econômica.
Uma das principais vantagens do uso da estrutura em alumínio é sua grande resistência à corrosão ambiental. Isto se deve ao fato do aparecimento imediatamente após a extrusão do perfil, de uma camada superficial fina, porém muito tenaz e inerte de óxido de alumínio.
Esta camada proporciona excelente proteção às camadas mais inferiores do metal possuindo ainda a característica de auto-regeneração quando afetada. As estruturas metálicas em alumínio natural ( sem pintura ou qualquer outro tipo de acabamento) são altamente recomendáveis para o uso em quase todos os ambientes industriais.
O produto da auto-oxidação do alumínio em contato com o ar é incolor e não tóxico, assim sendo, leva o alumínio a ser utilizado também em larga escala na indústria química e de alimentos.
O módulo de elasticidade do alumínio é 1/3 da do aço, por isso, as tensões devidas a impactos ou quedas que podem levar deformações às peças, são baixas. Por outro lado, este baixo coeficiente de elasticidade implica em cuidado especial na fase de cálculo, com as deformações globais e a estabilidade local das seções.
Ainda assim, mesmo com o coeficiente de condutibilidade térmica 2 vezes a do aço, as tensões oriundas das variações da temperatura são baixas, particularmente aquelas localizadas, onde a alta condutibilidade térmica do alumínio, reduz sobremaneira o gradiente térmico.
Outra grande vantagem da aplicação do alumínio na construção de estruturas ou veículos nas regiões árticas é que sob a influência de baixas temperaturas, as ligas em alumínio têm sua resistência aumentada e não sofrem o fenômeno da ruptura frágil.
Além da apresentação em chapas planas, o alumínio para estruturas é fornecido em perfis, sólidos (abertos) ou tubulares (fechados). Estes são fabricados pelo processo de extrusão em matrizes, cuja facilidade na concepção das mais variadas formas das seções, faz do alumínio um excelente material também de acabamento e decoração.
Modernamente, o uso de ferramentas CAD/CAM, faz da extrusão um dos mais ágeis, avançados e econômicos meios de fabricação de seções estruturais.
Devido às suas propriedades físicas o alumínio pode ser estampado, puncionado, usinado, cortado ou furado facilmente com máquinas operatrizes convencionais de alta velocidade. A união de peças estruturais pode ser feita tanto por aparafusamento como nas demais estruturas, ou alternativamente, utilizando-se o processo de rebitagem à frio. Este último, além de mais econômico, proporciona maior homogeneidade e beleza às ligações.
Em complementação ao “acabamento natural” geralmente empregado nos perfis para estruturas metálicas, alguns acabamentos especiais podem adicionar às peças de alumínio, grande beleza arquitetônica, tais como: texturização mecânica superficial, pintura, esmaltagem porcelanizada, anodização e outros. Particularmente às telhas, o uso do alumínio proporciona excepcional durabilidade, podendo estas ter acabamento natural, pintura, ou envernizamento.

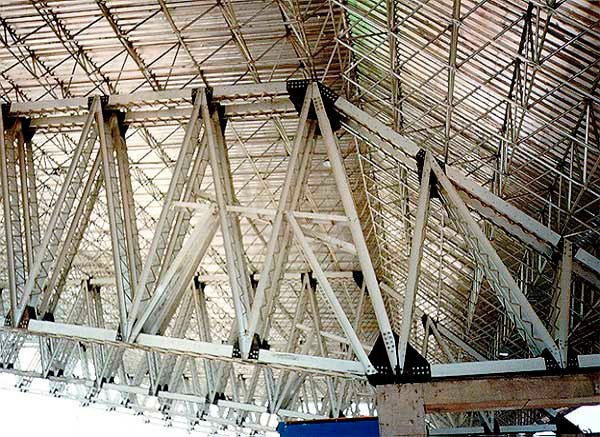